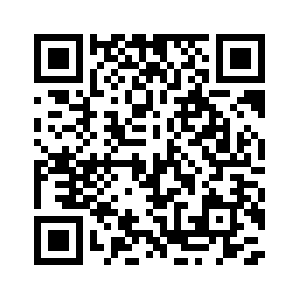
Abrasive Wear in Some High Fe-Cr-C Alloy in Cement Powder
Materials Science Energy SystemsMechanical Engineering受け取った 10 Oct 2024 受け入れられた 07 Jan 0225 オンラインで公開された 08 Jan 2025
Focusing on Biology, Medicine and Engineering ISSN: 2995-8067 | Quick Google Scholar
Next Full Text
Zinc Supplementation in Anorexic Children with Vomiting Syndrome: Evaluation from a Randomized Controlled Trial in Vietnam
受け取った 10 Oct 2024 受け入れられた 07 Jan 0225 オンラインで公開された 08 Jan 2025
The wear behavior in solid metallic materials is of high importance because of its connection with production cost. In this work, the behavior of wear and wear rate is shown in grinding balls produced from high Fe-Cr-C alloys produced by melting in medium frequency induction furnaces, and molding by automatic fleckless molding machine– Disamatic moldings machine. The total testing time is (12 hrs). The abrasive wear rate, which is the wear resistance multiplied by testing time in mg/Kg.hr. Two grinding balls of each of the three alloys: BC26, BC18, and BC13 are tested by rotating the balls with (50 Kg), cement powder inside a diesel working mixer of circular sections, inclined 45 and rotating by 30 rpm. Weighting and hardness testing results are found in the text, the chemical composition was tested by using spectra analyses type ARL 34000 OE. All the results obtained are shown in the tables and figures in the text. As a result, it can be stated that increasing Cr%, increases hardness, and decreases the wear rate, and the harder and higher the Cr% and C% it contains, the lower the wear rate and the higher wear resistance.
Wear is the damaging gradual removal or deformation of material at solid surfaces [
]. Abrasive wear is also defined as the loss of material due to hard particles that are forced against and move along a solid surface [ ]. Abrasive wear of metals occurs by plastic displacement of surface and the near-surface of material, martensitic steel with expected carbides in which the hardness of high C steels are high abrasion resistance [ , ]. Abrasive wear also occurs when a hard rough surface slides across a softer surface [ , ]. Abrasive wear plays a significant role in ore grinding in the absence of sulphites [ ]. Wear is the progressive loss of material resulting from the mechanical interaction of the two sliding surfaces under load [ ]. Annually a large amount of expenses is spent on industrial metal parts due to wear. The importance of wear research comes from that about 23% of the world's energy consumption originates from tribological contacts of which 20% is from overcoming friction, and 3% is from remanufacturing worn parts and spare equipment due to wear [ , ]. Worldwide, about 100 million Tera joules is used annually to overcome friction, and that is 20% of energy produced [ ]. The largest quantities of energy are used by industry, 29% and in transportation 27% [ ]. The wear process can be classified into different types according to tribological load and the materials involved i.e. abrasive, sliding, fritting wear, and material cavitations.Wear is caused by a number of mechanisms such as abrasive, adhesive, surface fatigue, and trip logical reaction. In abrasive micro cuttings, repeated plugging and fracture of the base body caused by the counter body asperities or by hard particles in the interfacial medium lead to wear [
].The main requirement of Portland cement is to have low iron content as Fe2O3 for white cement. Portland cement is one of the lowest-cost materials widely used over the last century [
]. Portland cement is obtained by heating the limestone, clay, and silica with some impurities at high temperatures in a rotating kiln, producing the clinker [ ]. Cement powder can be produced by milling the clinkers to the desired finesse using grinding balls [ , ]. Portland cement is extensively used in the construction of nuclear waste facilities. The hardness of materials is one of the most important mechanical properties in wear [ ].Hard material indicates high wear resistance, wear ranking, martensitic steels –Fe-Cr-C shoes high abrasive resistance such as silicate-aluminates-compound [
, ]. High Iron –Chromium-Carbon grinding balls are used in milling clinker by rotating on the axis of the mill [ ]. Chromium is extremely hard and it is the third hardest element behind Carbon and Boron [ ]. Chromium mostly chromites, produces Fe-Cr alloys with very high strength and forming hard solid solutions- carbides. The type of carbide form depends on the amount of carbon %, the higher the carbon content, the harder will be. High Cr–Fe, typically about 16%Cr results in high wear combined with high oxidation resistance [ , ]. The hardness of the material is one of the most important mechanical properties in wear and has been widely used as the criterion to determine abrasive wear resistance [ , ]. A metal with higher hardness has more wear resistance combined with higher mechanical strength [ ]. The more wear resistant a material is the less quickly it loses material from its surface [ ]. In other words, wear resistance refers to a material's ability to resist material loss by the same mechanical action. The wear of material has been characterized by weight loss and wear rate [ , ]. Abrasive wear testing conducted by many researchers mostly in wet conditions is according to ASTM [ - ] in 2016, 2020, and 2021 respectively. Grinding balls are used by the cement industry to transform the rock into fine cement. Abrasive wear is the result of friction between solid surfaces [ ].In the present work, a friction test of dry cement powder with high alloy Fe-Cr-C grinding balls of three grades of the given alloys is used through different periods of time running in a movable mixer. The weight in each period is checked and the wear rate is calculated by dividing the weight loss of each ball by its initial one.
The instruments used for the spectra–chemical testing were the spectra analyzer type ARL-34000-OE, and the mixer, for checking. The chemical compositions are shown in Table 1.
For weighing initial and individual weights an accurate weighing device was used. The results are presented in Tables 1-3.
The experiment starts by introducing the weighted grinding balls with 50 Kg of dry powder Portland cement in the mixer. The mixer then starts rotating with a speed of 30 rpm. The rotating mixer is inclined by 45ە in order to keep grinding balls rotating with cement freely. After every three hours, the mixer was stopped and cleaned and all grinding balls were weighed. The same procedure was repeated every three hours through 12 hrs of the test. All results are presented in Table 2. Differences in weight in each grinding ball during 12 hrs of the test are shown in Table 3. The mixer with grinding balls and cement powder is shown in Figure 1. The relation between the weights in all periods of the test is clear as shown in Figure 2.
The relation between Chromium contents and wear rates for the tested balls, as well as the hardness in HV units are presented in Figure 3.
The achieved results from testing the six grinding balls, whose chemical composition is revealed in Table 1. Each tow ball is from one alloy. The three alloys are BC26, BC18, and BC13. All of them contain high Cr% at different levels. The results reveal that the highest Cr% is in BC26 alloy and the lowest in BC13. All the tested balls are hard enough, they seem that they are quenching and tempering. Generally, their microstructures consist of eutectic Cr–carbide with secondary carbides and martensite with the rest of the impurities and retained austenite. The hardness of the balls increases as retained austenite decreases, and as Chromium and Carbon content increases, Cr has three main carbides, to form carbides, to increase corrosion and wear resistance, and to achieve the stable structure of the alloy at high temperatures. Abrasive wear of high Cr cast iron is lower than that of had field steel due to the presence of M7C3 carbides [
]. According to the above data, the wear rate or wear resistance is affected by the surface tested, Cr% and C% contents, and the hardness of tested grinding balls.The material loss from the three tested alloys during testing times is shown in Figure 2 and in Table 2. From that, it is clear that the loss in materials or the - wear - increased by the testing time, but in different amounts depending on the nature of the alloy i.e. less wear rate in BC26 (2.00 mg/Kg) and the most material loss in BC13 alloy (4.00 mg/Kg) due to the facts referred to in above. The relationship between Cr% and both wear rate and hardness is shown in Figure 3. It reveals that hardness in HV is directly proportional to the Cr% while the wear rate has two different stages of increasing. The first up to 16% the increments are slower than that of the higher (16-24)% of Cr. This can be explained because in the lower ranges of Cr, there may still be some amount of retained austenite in the structure, and by decomposition of retained austenite with increasing Cr%, faster precipitation of secondary Cr-carbides and martensite results from austenite decomposition, and both of them are harder than the first range, so faster decrement in wear rate is taking place.
By evaluating the results, the behavior of abrasive wear could be revealed. Finally, in Table 3 some small increases in hardness (40-20) HV can be observed, this may be due to plastic deformation accumulated on the ball surfaces. That hardness difference is more (40Hv) in BC26, (30Hv) in BC18 and the lowest in (20Hv) in BC13. After hardening and tempering the structure consists of Cr carbides martensite and traces of retained austenite; to ensure this fact, longer testing time is needed.
According to the results obtained from the tests and analyses, the following conclusions can be stated; The high hardness of Fe-Cr- C- alloys in cement milling grinding balls, results in low abrasive wear and high wear resistance. The microstructure consists of Cr carbides, Martensite, and traces of retained Austenite. The higher the Cr contents the lower the abrasive wear rate. To achieve a stable structure at high temperatures, it is used in the production of parts used where aggressive wear conditions. The higher C increases the formation of Cr Carbides.
At the finishing of this work, I would like to express my warm greetings to Amustaqbal University, my family, all colleagues, and Journal Editors and Reviewers with my best regards.
Chattopadhyay R. Surface wear: analysis, treatment, and prevention. ASM International-USA; 2001.
Standard terminology relating to wear and erosion. Annual Book of Standards, ASTM. 1987;3:243–250.
Shen G, Fang F, Kang C. Tribological performance of bioimplants: a comprehensive review. Nanotechnology and Precision Engineering (NPE). 2018;1(2):107–122.
Gupta B. Friction and wear mechanism of polymers, their composites and nanocomposites. In: Tribology of Polymers, Polymer Composites, and Polymer Nanocomposites. 2022:51–117.
Rabinowicz E. Friction wear of materials. John Wiley and Sons; 1965. Vol. 32:168–177.
The Editors of Encyclopaedia Britannica. Wear | Friction, adhesion & corrosion. Encyclopaedia Britannica. 1998 Jul 20. Retrieved from: https://www.britannica.com/science/wear
Iwasaki I, Riemer SC, Orlich JN, Natarajan KA. Corrosive and abrasive wear in ore grinding. Wear. 1985;103(3):253–267.
Mohammadnezhad M, Javaheri V. The effects of heat treatment on the mechanical properties of wear-resistant Cr-Mo steel. 2012.
Holmberg K, Erdemir A. Influence of tribology on global energy consumption, costs and emissions. Friction. 2017;5:263–284.
Holmberg K, Andersson P, Nylund NO, Mäkelä K, Erdemir A. Global energy consumption due to friction in trucks and buses. Tribology International. 2014;78:94–114.
Chicago Mercantile Exchange (CME). CME-Transaction-184-vol. 94, No. 3. 2016.
Holmberg K, Erdemir A. Global impact of friction on energy consumption, economy and environment. FME Transactions. 2015;43:181–185. Available from: https://www.mas.bg.ac.rs/_media/istrazivanje/fme/vol43/3/01_kholmberg.pdf
Kovaříková I, Szewczyková B, Blaškovitš P, Hodúlová E, Lechovi E. Study and characteristic of abrasive wear mechanisms. Retrieved from: https://www.semanticscholar.org/paper/STUDY-AND-CHARACTERISTIC-OF-ABRASIVE-WEAR-Szewczykov%C3%A1-Bla%C5%A1kovit%C5%A1/35d05689f176bb64e7e69713519912025a2bce12
Yuan Q, Liu Z, Zheng K, Ma C. Civil Engineering Materials: From Theory to Practice. Elsevier; 2021.
Samui P, Kim D, Iyer NR, Chaudhary S, editors. New materials in civil engineering. Butterworth-Heinemann; 2020.
Wang Y, AL‐Huqail AA, Salimimoghadam S, Jasim Mohammed K, Jan A, Ali HE, et al. The metaheuristic optimization of the mechanical properties of sustainable energies using artificial neural networks and genetic algorithm: A case study by eggshell fine waste. Int J Energy Res. 2022;46(15):21338–21352.
Harrisson AM. Constitution and specification of Portland cement. In: Lea’s Chemistry of Cement and Concrete. 501.
Ojovan MI. Handbook of advanced radioactive waste conditioning technologies. Woodhead Publishing; 2011.
Liew MS, Nguyen-Tri P, Nguyen TA, Kakooei S, editors. Smart nanoconcretes and cement-based materials: properties, modelling and applications. Elsevier; 2019.
Moore D. Cement kilns: clinker thermochemistry. Retrieved from: https://www.cementkilns.co.uk/ckr_therm.html. Accessed 6 Mar 2014.
Del Strother P. Manufacture of Portland cement. In: Lea’s Chemistry of Cement and Concrete. 1:31–56; 2019.
Institute of Materials, Minerals and Mining (IOM3). Element focus: Chromium. Retrieved from: https://www.iom3.org/resource/element-focus-chromium-pdf.html. September 2020.
High Chromium Cast Iron: Part One | Total Materia. Retrieved from: https://www.totalmateria.com/en-us/articles/high-chromium-cast-iron-1/. August 2017.
Pawar S, Jha AK, Mukhopadhyay G. Effect of different carbides on the wear resistance of Fe-based hardfacing alloys. Int J Refractory Metals Hard Mater. 2019;78:288–295.
Jeong DH, Erb U, Aust KT, Palumbo G. The relationship between hardness and abrasive wear resistance of electrodeposited nanocrystalline Ni–P coatings. Scripta Mater. 2003;48(8):1067–1072.
Khidhair JM. Investigation of high speed steel (R18). IJRDO J Mech Civ Eng. 2019;5(4). Retrieved from: https://www.ijrdo.org/index.php/mce/issue/view/507
Rojacz H, Katsich C, Kirchgaßner M, Kirchmayer R, Badisch E. Impact-abrasive wear of martensitic steels and complex iron-based hardfacing alloys. Wear. 2022;492–493:204183.
High Chromium Cast Iron: Part One | Total Materia. Retrieved from: https://www.totalmateria.com/en-us/articles/high-chromium-cast-iron-1/.
Pawar S, Jha AK, Mukhopadhyay G. Effect of different carbides on the wear resistance of Fe-based hardfacing alloys. Int J Refractory Metals Hard Mater. 2019;78:288–295.
World Energy Outlook 2013 – Analysis - IEA. Retrieved from: https://www.iea.org/reports/world-energy-outlook-2013. November 1, 2013.
Zsidai L, Kátai L. Abrasive wear and abrasion testing of PA 6 and PEEK composites in small-scale model system. Acta Polytech Hungarica. 2016.
Paz-Triviño F, Buitrago-Sierra R, Santa-Marín JF. Wear resistance and hardness of nanostructured hardfacing coatings. Dyna. 2020;87(214):146–154. Retrieved from: https://www.scielo.org
Coatings H. Tests & Analysis - Hardide Coatings. Retrieved from: https://hardide.com/technical-information/hardide-surface-coating-tests/. September 6, 2021.
Aissat S, Zaid M, Sadeddine A. Correlation between hardness and abrasive wear of grinding balls. Metall Res Technol. 2020;117(6):608.
Atabaki MM, Jafari S, Abdollah-pour H. Abrasive wear behavior of high chromium cast iron and Hadfield steel—a comparison. J Iron Steel Res Int. 2012;19(4):43–50.
Mohammed KJ. Abrasive Wear in Some High Fe-Cr-C Alloy in Cement Powder. IgMin Res. January 08, 2025; 3(1): 011-014. IgMin ID: igmin278; DOI:10.61927/igmin278; Available at: igmin.link/p278
次のリンクを共有した人は、このコンテンツを読むことができます:
Air-Conditioning and Refrigeration Technical Deparment, Almustaqbal University, Babylon, Hilla City, Iraq
Address Correspondence:
Dr. Khidhair Jasim Mohammed, Assistant Professor, Engineer, Air-Conditioning and Refrigeration Technical Deparment, Almustaqbal University, Babylon, Hilla City, Iraq, Email: [email protected]; [email protected]
How to cite this article:
Mohammed KJ. Abrasive Wear in Some High Fe-Cr-C Alloy in Cement Powder. IgMin Res. January 08, 2025; 3(1): 011-014. IgMin ID: igmin278; DOI:10.61927/igmin278; Available at: igmin.link/p278
Copyright: This is an open access article distributed under the Creative Commons Attribution License, which permits unrestricted use, distribution, and reproduction in any medium, provided the original work is properly cited.
Chattopadhyay R. Surface wear: analysis, treatment, and prevention. ASM International-USA; 2001.
Standard terminology relating to wear and erosion. Annual Book of Standards, ASTM. 1987;3:243–250.
Shen G, Fang F, Kang C. Tribological performance of bioimplants: a comprehensive review. Nanotechnology and Precision Engineering (NPE). 2018;1(2):107–122.
Gupta B. Friction and wear mechanism of polymers, their composites and nanocomposites. In: Tribology of Polymers, Polymer Composites, and Polymer Nanocomposites. 2022:51–117.
Rabinowicz E. Friction wear of materials. John Wiley and Sons; 1965. Vol. 32:168–177.
The Editors of Encyclopaedia Britannica. Wear | Friction, adhesion & corrosion. Encyclopaedia Britannica. 1998 Jul 20. Retrieved from: https://www.britannica.com/science/wear
Iwasaki I, Riemer SC, Orlich JN, Natarajan KA. Corrosive and abrasive wear in ore grinding. Wear. 1985;103(3):253–267.
Mohammadnezhad M, Javaheri V. The effects of heat treatment on the mechanical properties of wear-resistant Cr-Mo steel. 2012.
Holmberg K, Erdemir A. Influence of tribology on global energy consumption, costs and emissions. Friction. 2017;5:263–284.
Holmberg K, Andersson P, Nylund NO, Mäkelä K, Erdemir A. Global energy consumption due to friction in trucks and buses. Tribology International. 2014;78:94–114.
Chicago Mercantile Exchange (CME). CME-Transaction-184-vol. 94, No. 3. 2016.
Holmberg K, Erdemir A. Global impact of friction on energy consumption, economy and environment. FME Transactions. 2015;43:181–185. Available from: https://www.mas.bg.ac.rs/_media/istrazivanje/fme/vol43/3/01_kholmberg.pdf
Kovaříková I, Szewczyková B, Blaškovitš P, Hodúlová E, Lechovi E. Study and characteristic of abrasive wear mechanisms. Retrieved from: https://www.semanticscholar.org/paper/STUDY-AND-CHARACTERISTIC-OF-ABRASIVE-WEAR-Szewczykov%C3%A1-Bla%C5%A1kovit%C5%A1/35d05689f176bb64e7e69713519912025a2bce12
Yuan Q, Liu Z, Zheng K, Ma C. Civil Engineering Materials: From Theory to Practice. Elsevier; 2021.
Samui P, Kim D, Iyer NR, Chaudhary S, editors. New materials in civil engineering. Butterworth-Heinemann; 2020.
Wang Y, AL‐Huqail AA, Salimimoghadam S, Jasim Mohammed K, Jan A, Ali HE, et al. The metaheuristic optimization of the mechanical properties of sustainable energies using artificial neural networks and genetic algorithm: A case study by eggshell fine waste. Int J Energy Res. 2022;46(15):21338–21352.
Harrisson AM. Constitution and specification of Portland cement. In: Lea’s Chemistry of Cement and Concrete. 501.
Ojovan MI. Handbook of advanced radioactive waste conditioning technologies. Woodhead Publishing; 2011.
Liew MS, Nguyen-Tri P, Nguyen TA, Kakooei S, editors. Smart nanoconcretes and cement-based materials: properties, modelling and applications. Elsevier; 2019.
Moore D. Cement kilns: clinker thermochemistry. Retrieved from: https://www.cementkilns.co.uk/ckr_therm.html. Accessed 6 Mar 2014.
Del Strother P. Manufacture of Portland cement. In: Lea’s Chemistry of Cement and Concrete. 1:31–56; 2019.
Institute of Materials, Minerals and Mining (IOM3). Element focus: Chromium. Retrieved from: https://www.iom3.org/resource/element-focus-chromium-pdf.html. September 2020.
High Chromium Cast Iron: Part One | Total Materia. Retrieved from: https://www.totalmateria.com/en-us/articles/high-chromium-cast-iron-1/. August 2017.
Pawar S, Jha AK, Mukhopadhyay G. Effect of different carbides on the wear resistance of Fe-based hardfacing alloys. Int J Refractory Metals Hard Mater. 2019;78:288–295.
Jeong DH, Erb U, Aust KT, Palumbo G. The relationship between hardness and abrasive wear resistance of electrodeposited nanocrystalline Ni–P coatings. Scripta Mater. 2003;48(8):1067–1072.
Khidhair JM. Investigation of high speed steel (R18). IJRDO J Mech Civ Eng. 2019;5(4). Retrieved from: https://www.ijrdo.org/index.php/mce/issue/view/507
Rojacz H, Katsich C, Kirchgaßner M, Kirchmayer R, Badisch E. Impact-abrasive wear of martensitic steels and complex iron-based hardfacing alloys. Wear. 2022;492–493:204183.
High Chromium Cast Iron: Part One | Total Materia. Retrieved from: https://www.totalmateria.com/en-us/articles/high-chromium-cast-iron-1/.
Pawar S, Jha AK, Mukhopadhyay G. Effect of different carbides on the wear resistance of Fe-based hardfacing alloys. Int J Refractory Metals Hard Mater. 2019;78:288–295.
World Energy Outlook 2013 – Analysis - IEA. Retrieved from: https://www.iea.org/reports/world-energy-outlook-2013. November 1, 2013.
Zsidai L, Kátai L. Abrasive wear and abrasion testing of PA 6 and PEEK composites in small-scale model system. Acta Polytech Hungarica. 2016.
Paz-Triviño F, Buitrago-Sierra R, Santa-Marín JF. Wear resistance and hardness of nanostructured hardfacing coatings. Dyna. 2020;87(214):146–154. Retrieved from: https://www.scielo.org
Coatings H. Tests & Analysis - Hardide Coatings. Retrieved from: https://hardide.com/technical-information/hardide-surface-coating-tests/. September 6, 2021.
Aissat S, Zaid M, Sadeddine A. Correlation between hardness and abrasive wear of grinding balls. Metall Res Technol. 2020;117(6):608.
Atabaki MM, Jafari S, Abdollah-pour H. Abrasive wear behavior of high chromium cast iron and Hadfield steel—a comparison. J Iron Steel Res Int. 2012;19(4):43–50.